Needs Analysis Overview
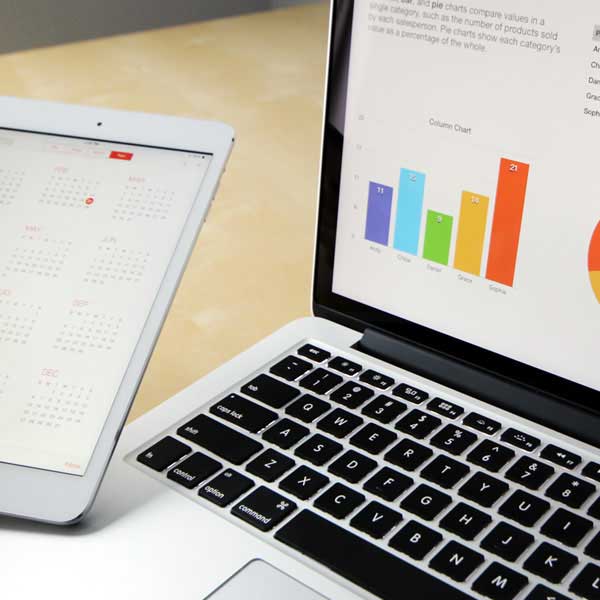
Once your goals are defined and the engineering design information is collected, Dayton T. Brown, Inc.’s logisticians will perform a thorough needs analysis and develop required reports, which may include:
- Failure Modes, Effects, and Criticality Analysis (FMECA)
- Maintainability analysis and Mean Time to Repair (MTTR) predictions
- Failure Reporting, Analysis, and Corrective Action System (FRACAS)
- Manpower Requirements Analysis/Human Engineering Analysis (MRA/HEA)
- Fault Tree Analysis (FTA)
- Provisioning technical documentation
- Hazard tracking and risk resolution
- Reliability analysis and Mean Time Between Failure (MTBF) predictions
- Level of Repair Analysis (LORA)
- Reliability-Centered Maintenance Analysis (RCMA)
- Logistics Support Analysis (LSA)
- System Safety Analysis (SSA)
- Logistics Support Analysis Record (LSAR)
- Training needs analysis and assessment
Needs Analysis Deliverables
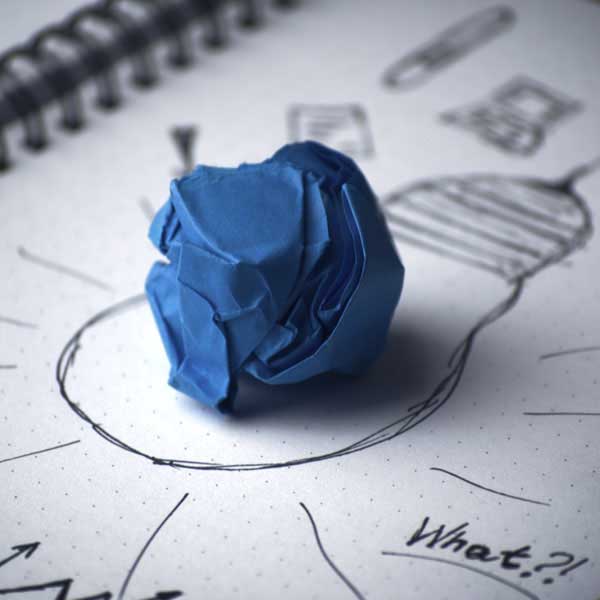
Product Support Integration (PSI)
A product’s life cycle is one of the cornerstones of a manufacturer’s Information Technology (IT) structure. DTB can describe the engineering aspect of a product, managing its description and properties throughout its development and useful life.
PSI delivers performance outcomes as defined by the performance metrics of a system or product. The integration task commits to this performance level at a lower cost or at increased performance costs, similar to those previously achieved under non-Performance-Based Logistics (PBL) or transactional portfolios of product support arrangements for goods and services.
PBL systems help organizations grapple with the increasing complexity and engineering challenges of developing new products for global markets, as well as compliance with military and governmental requirements.
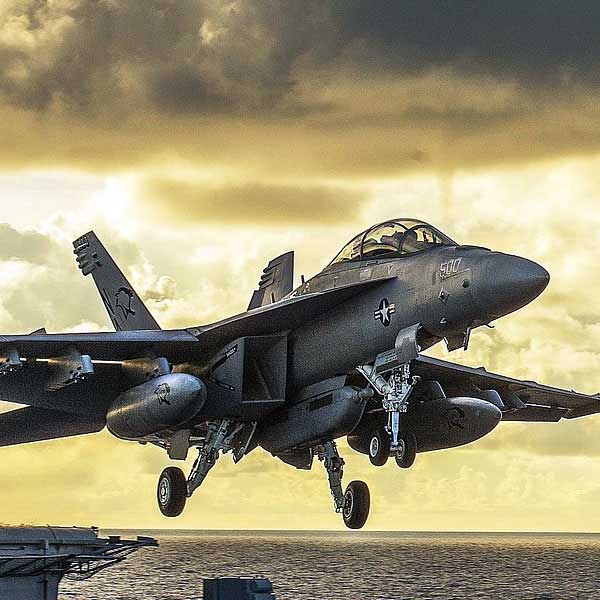
The DoD & Performance-Based Logistics (PBL)
PBL is the DoD’s preferred approach to supporting weapon system logistics. This concept seeks to deliver product support as an integrated, affordable performance package that is designed to optimize system readiness. PBL meets performance goals for a weapon system through a support structure that is based on long-term performance agreements with clear lines of authority and responsibility.
DoD program managers are required to develop and implement performance-based life cycle product support strategies for weapon systems. These strategies should optimize total system availability, while minimizing costs and the logistics footprint. Within the commercial marketplace, logistics analysis is known as PSA, as defined by the Society of Automotive Engineers (SAE).
The selection of the specific performance metrics should be carefully considered and supported by an operationally-oriented analysis, taking into account technology maturity, fiscal constraints, and schedule. The metrics should also be appropriate to the scope of the PSIs and the provider’s responsibilities.
Systems should be reviewed to ensure that they are motivating the desired behaviors across the enterprise. PBL gives contractors partial responsibility for readiness. The Defense Logistics Agency (DLA) is working to combine multiple service contracts for similar items into a single PBL arrangement that supports all of the services.